SOLUBLE SALTS REACTIONS ARE VISIBLE WITH TIME
As in many areas of corrosion control, we have entered a new phase in surface preparation for protective coatings. For decades, surface preparation specifications primarily stipulated a visually interpreted condition. Today, the industry refers to non-visible surface requirements with more and more frequency. Aside from greases and oils, these new non-visible requirements are related to soluble salts. Many people in the coating industry, including facility owners, applicators and inspectors, are somewhat stymied by these requirements. Often they are ignored on the jobsite because they require time, cost money, or neither the contractor nor the inspector understands the need to meet the specification, which includes something they can not see. (Out of sight, out of mind?)
What is widely unknown and not understood is what occurs when soluble salts are left on a surface prior to coating application. Soluble salts, primarily chlorides and/or sulfates, are hygroscopic by nature. This means they draw moisture. In fact, they draw moisture so well that these salts will draw moisture right through a coating film. Some coatings are less permeable than others, some are applied thicker than others, but the end result is the same; Salts will draw moisture through any liquid applied coating eventually. That moisture, complexed with the salts left on a surface, makes a very good electrolyte and sets up an active corrosion cell beneath the coating, right on the very surface the coating is to protect. While industry has not determined what levels of salts are “acceptable”, it has been established that any amount of soluble salt is detrimental to the overall lifespan of the coating.
Though we cannot see chlorides or sulfates on a steel surface, we can see the result of their presence in a very short time span, usually a matter of hours. Photo 1 shows six (6) steel panels, 3″ x 6″, that were exposed to a five percent (5%) sodium chloride solution in a salt fog cabinet for a period of approximately fourteen (14) days. Note that the rust is uniformly distributed over the entire surface of each panel. Photo 2 is the same six (6) panels after being abrasive blasted to Near White Metal.
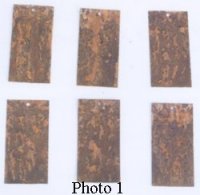
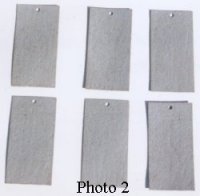
Immediately after the abrasive blasting was completed, the panel shown in Photo 3 was washed with tap water with a 3000 p.s.i. pressure washer. The photograph was taken 24 hours after washing. Another panel, shown in Photo 4, was washed in the same manner, but a 1% soluble salt remover was added. This photograph was also taken 24 hours later. Photo 5 shows a control panel exposed only to atmospheric humidity for 24 hours, then photographed.
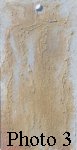
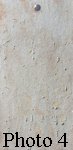
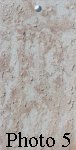
As seen in Photo 5, the salts are concentrated at the corroded areas. Note that in and around the pitted areas the salts have formed an electrochemical attachment to the steel that abrasive blasting did not remove. Had the surface been coated immediately after abrasive blasting, those salts would now be beneath the coating and the mechanism for a premature failure would already be underway. NOTE: This photograph also shows how testing performed at a specific location can offer differing results from another test at a very near proximity. Each test performed is specific to the locale being tested. It is also evident in the same photograph why it is recommended to perform testing at pitted locations rather than at a flat non-corroded location.
As seen in Photo 3, the salts are now not only concentrated in and around the pitted locations, but the addition of the pressure wash with tap water has not removed them and has actually caused them to spread over a larger area of the surface. Again, had this surface been coated immediately after washing, the corrosion mechanism would be in place and underway.
Photo 4 shows that the addition of the soluble salt remover has actually removed the salt, as evidenced by the lack of a corrosion reaction. What is also visible is the “operator error”. The operator who washed this panel did not wash 100% of the surface adequately, but even with that operator error, the minimal rust back indicates that there are only minor amounts of salt left, as evidenced by the very slight corrosion reaction after 24 hours. Were this panel coated immediately after washing, the ultimate coating performance would be far more successful than either of the other two samples.
Many specifiers are very aware of just how detrimental soluble salts are, while others simply have not yet learned. Hopefully, this visible evidence will help them understand the need to address non-visible requirements in specifications.